The relentless pursuit of computational power in cryptocurrency mining inherently generates a substantial amount of heat, a fundamental byproduct of energy conversion. For anyone operating mining rigs, whether a compact home setup or a larger array, effectively dissipating this thermal energy is not merely an operational nicety; it is a critical determinant of system stability, longevity, and overall profitability. Overlooking robust thermal management can lead to a cascade of detrimental effects, including reduced hashing performance due to thermal throttling, premature component failure, increased power consumption as fans spin at maximum speeds, and an escalation in operational noise levels. As mining hardware becomes increasingly dense and powerful, the heat output per unit area continues to climb, making innovative and effective cooling solutions paramount. This article delves deeply into practical, do-it-yourself strategies for managing miner heat, exploring various methodologies from optimizing airflow to advanced immersion techniques, all while emphasizing cost-effectiveness, safety, and long-term sustainability.
Understanding the fundamental principles of heat transfer is the cornerstone of designing an effective cooling system for your mining hardware. Heat, in essence, always seeks to move from a warmer area to a cooler one. This natural phenomenon occurs through three primary mechanisms: conduction, convection, and radiation. In the context of a mining rig, internal components like the graphics processing units (GPUs) or application-specific integrated circuits (ASICs) generate heat directly within their silicon dies. This heat then conducts through the integrated heat spreader (IHS) or the directly mounted cooling solution to a heat sink. From the heat sink, it is primarily transferred via convection into the surrounding air, which then carries the heat away. Radiation also plays a minor role, as components radiate heat directly to their surroundings, but its contribution is typically less significant than conduction and convection in a typical air-cooled setup. Optimizing these transfer paths is key to efficient heat removal, ensuring that the thermal energy generated by active components is swiftly moved away from sensitive electronics and ultimately expelled from the mining environment.
Effective heat dissipation directly translates into tangible benefits for the mining operation. Firstly, it prevents thermal throttling, a self-preservation mechanism where hardware automatically reduces its clock speed and power consumption to lower temperatures when thresholds are exceeded. This directly impacts mining profitability by decreasing the hash rate, meaning fewer attempts at solving cryptographic puzzles and thus fewer potential rewards. Secondly, consistent operation within optimal temperature ranges significantly extends the lifespan of expensive mining hardware. Every additional degree Celsius above a component’s ideal operating temperature can accelerate degradation, leading to premature failures of GPUs, memory modules, power delivery systems, and even ASICs. Industry data suggests that a sustained 10-degree Celsius reduction in GPU core temperature can extend its operational lifespan by as much as 20% to 30%. Thirdly, efficient cooling can lead to lower overall power consumption. When components run cooler, their integrated fans often don’t need to spin as fast, reducing their individual power draw. Moreover, preventing throttling means the hardware operates at its peak efficiency more consistently, reducing the waste of energy on suboptimal performance. Lastly, reduced fan speeds directly correlate with lower acoustic output, creating a more tolerable operational environment, especially pertinent for home-based mining setups.
Fundamentals of Air Cooling for Mining Rigs
Air cooling remains the most common and accessible method for heat dissipation in DIY mining setups, primarily due to its simplicity, lower initial cost, and ease of implementation. However, achieving optimal performance with air cooling goes far beyond simply pointing a fan at your rig. It involves a meticulous approach to airflow management, fan selection, and environmental control.
Optimizing Airflow within the Mining Enclosure
The efficiency of air cooling hinges entirely on how effectively cool air is introduced to the heat-generating components and how efficiently hot air is exhausted. Without proper airflow pathways, hot air can recirculate within the enclosure, leading to localized hot spots and a general increase in ambient temperature, thereby diminishing cooling efficacy.
* Intake and Exhaust Balance: A fundamental principle is to create a balanced airflow system, ideally with slightly positive or negative pressure depending on the setup. A positive pressure system, where intake volume exceeds exhaust volume, helps prevent dust ingress by forcing air out through all available gaps. Conversely, a negative pressure system, where exhaust volume is greater, efficiently removes heat but can draw in unfiltered air from various openings. For most DIY setups, a balanced approach or slightly positive pressure is often ideal, prioritizing clean air delivery to sensitive components.
* Directing Airflow: Simply having powerful fans is insufficient if the air isn’t channeled correctly. Hot air naturally rises, so positioning exhaust fans at the top or rear of an enclosure and intake fans at the bottom or front is a standard and effective strategy. Furthermore, using baffles or custom shrouds made from materials like acrylic or sheet metal can force air directly over heatsinks and GPUs, preventing it from bypassing critical components. Imagine a scenario where a GPU’s integrated cooler is pulling air from an open space; if that open space is filled with already warm, stagnant air, the cooling potential is significantly reduced. Custom ducts can ensure that only fresh, cooler air is fed into the GPU’s heatsink.
* Minimizing Obstructions: Cables, power supplies, and other ancillary components can significantly impede airflow. Careful cable management, using zip ties or Velcro straps to bundle and route cables neatly out of the airflow path, is crucial. Similarly, consider the placement of power supply units (PSUs); while some are designed to be an exhaust component, others can block crucial intake or exhaust vents.
Strategic Fan Selection and Placement
Not all fans are created equal, and choosing the right type for specific applications within your cooling scheme is paramount. Fan specifications like Cubic Feet per Minute (CFM) and Static Pressure (SP) are critical considerations.
* CFM (Cubic Feet per Minute): This metric indicates the volume of air a fan can move. High-CFM fans are ideal for moving large volumes of air in open or less restrictive environments, such as general case ventilation where there’s little impedance to airflow.
* Static Pressure (SP): Measured in millimeters of water (mmH2O), static pressure indicates a fan’s ability to push air through restrictive elements like dense radiator fins, tight dust filters, or narrow ducts. Fans with high static pressure are essential when air needs to be forced through resistance. For instance, cooling a tightly packed array of GPUs or a radiator for a liquid cooling loop demands fans with high static pressure capabilities.
* Axial vs. Centrifugal (Blower) Fans:
* Axial fans, the most common type, move air parallel to the fan’s axis of rotation. They are excellent for high airflow (CFM) in relatively unrestricted environments. Most case fans and GPU fans are axial.
* Centrifugal fans, often called blower fans, draw air in parallel to the motor and expel it perpendicularly, often through a concentrated opening. They excel at generating high static pressure and are ideal for pushing air through restrictive pathways or directing airflow in a very focused manner, such as in certain ASIC miners or some industrial server enclosures.
* Fan Size and Noise: Larger fans typically move more air at lower RPMs, resulting in less noise compared to smaller fans moving the same volume of air. Opting for 120mm or 140mm fans where space permits is generally preferable to smaller, faster-spinning 80mm or 92mm fans. Also, look for fans with Fluid Dynamic Bearings (FDB) or Magnetic Levitation (ML) bearings, as these are quieter and more durable than sleeve or ball bearings.
* Push-Pull Configurations: For cooling radiators or dense arrays, a “push-pull” configuration, where fans are mounted on both sides of the cooling element, can significantly improve heat dissipation. One set of fans pushes air through, while the other pulls it through, increasing effective airflow and static pressure. This can lead to a 10-15% improvement in cooling efficiency over a single-sided setup.
* Fan Speed Control: Implementing PWM (Pulse Width Modulation) controlled fans with a fan controller or motherboard headers allows dynamic adjustment of fan speeds based on temperature, reducing noise and power consumption when full cooling power isn’t needed. DIY solutions often involve microcontrollers like Arduino or Raspberry Pi to manage fan speeds based on sensor readings.
DIY Air Ducting and Plenums for Targeted Cooling
In a crowded mining rig or a server rack, simply relying on general airflow can be inefficient. Custom air ducting and plenums can precisely direct cool air to specific components and efficiently channel hot air away.
* Materials: Common DIY materials include corrugated plastic sheets (e.g., coroplast), thin aluminum sheets, or even rigid cardboard for prototyping. For more permanent solutions, ABS plastic sheets or thin plywood can be used. Seals can be created with foam strips or silicone caulk.
* Design Principles:
* Hot Air Exhaust Plenum: Building a sealed box or duct around the exhaust side of GPUs or ASICs allows all the hot air they expel to be consolidated and directed out of the enclosure via a single, powerful exhaust fan or duct. This prevents hot air from recirculating.
* Cold Air Intake Plenum: Similarly, a plenum can be built on the intake side, ensuring that fans draw only cool, fresh air from outside the enclosure and distribute it evenly across all components.
* Individual GPU Shrouds: For open-air rigs, individual acrylic or plastic shrouds can be crafted to encase each GPU, forcing its fans to draw air from a specific direction (e.g., from the front of the rig) and exhaust it towards the rear. This creates mini-tunnels for each card, significantly enhancing their cooling performance.
* Negative Pressure Tunnels for ASICs: Some DIY ASIC cooling solutions involve creating a sealed tunnel around the ASIC’s intake and exhaust, connecting the intake directly to a source of cool air and the exhaust to a powerful external fan, creating an isolated, high-airflow path specifically for the ASIC. This approach has been shown to reduce ASIC temperatures by 5-8 degrees Celsius consistently in a test environment.
Addressing Ambient Air Temperature Challenges
The temperature of the air drawn into your mining setup fundamentally limits how cool your components can get. If your ambient air is already hot, even the most efficient internal cooling system will struggle.
* Dedicated Ventilation Systems: For indoor setups, especially in smaller rooms or garages, a dedicated ventilation system is crucial. This involves installing an exhaust fan (like an inline duct fan used in hydroponics) that actively pulls hot air out of the mining space and pipes it outdoors or to another area. Simultaneously, ensuring an adequate source of cooler intake air, perhaps from another room or a filtered outdoor vent, is essential. For example, a 6-inch inline duct fan rated at 400 CFM can effectively ventilate a 100 sq ft room with a constant air exchange.
* Portable Air Conditioning Units: In very hot climates, supplementary cooling for the entire room might be necessary. Portable air conditioning units can be effective, but remember their exhaust must be vented outdoors, and they consume significant power. They can lower ambient room temperature by 5-10 degrees Celsius, which translates directly to component temperature reductions.
* Evaporative Coolers (Swamp Coolers): In arid climates with low humidity, evaporative coolers offer a more energy-efficient alternative to AC. They work by passing hot, dry air over water-soaked pads, cooling the air through evaporation. While effective at reducing air temperature by 5-15 degrees Celsius in suitable climates, they add humidity, which can be detrimental to electronics in certain environments. Proper humidity monitoring and management are vital if considering this option.
* Basement or Cooler Room Placement: If available, locating mining rigs in the coolest part of a building, such as a basement or a dedicated utility room with good ventilation, can provide a natural advantage.
Passive Cooling Strategies and Dust Management
While active cooling (fans, liquid) handles the bulk of heat dissipation, passive strategies can supplement and improve overall thermal performance.
* Larger Heatsinks: In some cases, replacing stock GPU heatsinks with larger aftermarket air coolers (often designed for gaming PCs) can significantly improve passive heat dissipation area, reducing the reliance on high fan speeds. While a more involved DIY project, such modifications can lead to a 10-15% reduction in core temperatures under load.
* Heat Spreader Contact: Ensuring optimal contact between the heat source (GPU/ASIC die, VRAM, VRMs) and the heatsink is crucial. High-quality thermal paste or thermal pads, applied correctly, dramatically improve heat transfer through conduction. Regular inspection and replacement of thermal interface materials (TIM) every 12-18 months can maintain peak thermal performance.
* Dust Management: Dust acts as an insulating layer, trapping heat and impeding airflow. Implementing robust dust filtration at all intake points is non-negotiable. DIY filter frames can be made from wood or plastic, holding readily available furnace filters or specialized electrostatic filter media. Regular cleaning of filters (weekly or bi-weekly depending on dust levels) and internal components (monthly air dusting) is essential. A 1mm layer of dust can degrade heatsink efficiency by up to 5%, leading to noticeable temperature increases.
Advanced DIY Liquid Cooling Solutions
When air cooling reaches its limits, especially with high-density mining hardware or in environments where noise is a significant concern, liquid cooling becomes a compelling alternative. While more complex to implement in a DIY setting, it offers superior thermal performance, quieter operation, and the ability to transfer heat more effectively over longer distances.
Introduction to Open-Loop vs. Closed-Loop Systems
* Closed-Loop Systems (AIOs): All-In-One (AIO) liquid coolers are factory-sealed units typically used for CPUs, consisting of a pump, cold plate, radiator, and tubing. While simple, adapting them for multiple GPUs or ASICs is challenging due to their fixed design. However, an individual AIO can be used for a single, high-power GPU if a compatible bracket or modification exists.
* Open-Loop Systems (Custom Loops): These are fully customizable systems where you select each component: pump, reservoir, cold plates (water blocks), radiator, tubing, and fittings. This DIY approach offers maximum flexibility and superior performance, allowing you to cool multiple components in a single loop. It’s the focus of advanced DIY liquid cooling for miners.
Component Selection for DIY Liquid Loops
Building a custom liquid cooling loop requires careful consideration of each component’s specifications and compatibility.
* Pumps: The pump is the heart of the loop, circulating the coolant.
* D5 Pumps: Renowned for their reliability, quiet operation, and strong flow rates. They are often integrated with reservoirs. A single D5 pump can typically handle a loop cooling 2-4 GPUs and a large radiator efficiently.
* DDC Pumps: More compact and offer higher static pressure, making them suitable for loops with significant flow restriction (e.g., multiple water blocks, restrictive radiators). They can be slightly noisier than D5s.
* Flow Rate (L/min) vs. Head Pressure (meters): Understanding these specs is crucial. Flow rate indicates how much fluid the pump can move, while head pressure indicates its ability to push against resistance. A balanced approach is needed depending on your loop’s complexity.
* Radiators: The primary heat exchange component, where heat from the coolant is transferred to the ambient air.
* Size (mm): Common sizes are 120mm, 240mm, 360mm, 480mm, 560mm, and even larger (e.g., 1080mm for extreme builds). The more surface area, the better the heat dissipation. A general rule of thumb is to have at least 120mm of radiator length per component being cooled (e.g., 360mm for three GPUs), plus an additional 120mm for overhead.
* Thickness (mm): Thicker radiators (e.g., 45mm, 60mm) hold more coolant and can dissipate more heat, but they require higher static pressure fans.
* Fin Density (FPI – Fins Per Inch): Higher FPI radiators offer more surface area but are more restrictive, necessitating high static pressure fans. Lower FPI radiators are less restrictive and work well with lower RPM, higher CFM fans.
* Material: Copper is the standard for high-performance radiators due to its excellent thermal conductivity. Avoid mixing metals (e.g., aluminum radiators with copper blocks) to prevent galvanic corrosion.
* Reservoirs: Hold excess coolant, aid in filling the loop, and help with air bubble removal. Sizes vary widely, with larger reservoirs making the filling and bleeding process easier. They can be standalone or integrated with pumps.
* Tubing: Carries the coolant between components.
* Material: PVC (flexible, economical), EPDM (flexible, durable, opaque, virtually no plasticizer leaching), PETG/Acrylic (rigid, clear, aesthetically pleasing, requires heat bending).
* Diameter (ID/OD): Inner Diameter (ID) and Outer Diameter (OD). Common sizes include 3/8″ ID x 5/8″ OD for soft tubing, and 12mm, 14mm, 16mm OD for rigid tubing. Larger IDs generally allow for greater flow rates with less restriction.
* Fittings: Connect tubing to components.
* Compression Fittings: Provide a secure, leak-proof seal for both soft and rigid tubing. Highly recommended.
* Barbs: Simpler, less expensive fittings for soft tubing, secured with hose clamps. Less secure than compression fittings.
* Rotary/Angled Fittings: Allow for cleaner routing and easier installation in tight spaces.
* Coolants: Specialized fluids designed for liquid cooling.
* Types: Clear (distilled water with additives), colored, pastel.
* Additives: Anti-corrosion (crucial for protecting metal components), anti-algae/biocide (prevents organic growth). Pre-mixed coolants already contain these. Distilled water alone is not recommended for long-term use due to lack of corrosion protection and biological growth potential.
* Maintenance: Coolant typically needs to be flushed and replaced every 12-24 months, depending on the coolant type and system cleanliness.
DIY Water Blocks for GPUs/ASICs
While off-the-shelf water blocks are available for many popular GPUs, they can be expensive, and finding them for less common or older ASICs can be challenging. DIY water blocks are generally not recommended due to the precision required for good thermal contact and sealing, but some highly skilled individuals undertake such projects.
* Feasibility and Risks: Creating a custom water block requires precise machining (CNC router, laser cutter) of copper or aluminum, meticulous design for internal flow paths, and robust sealing mechanisms. The risks include poor thermal contact leading to overheating, and leaks causing catastrophic damage to electronics.
* Alternatives for ASICs: Instead of full water blocks, some DIY ASIC cooling strategies involve modifying existing heatsinks to integrate a small liquid-cooled plate, or directly submerging the entire hashboard in dielectric fluid (immersion cooling), which is a more viable DIY liquid cooling strategy for ASICs.
* Modified GPU Coolers: A more common DIY approach for GPUs that lack specific water blocks is to adapt existing CPU AIOs by carefully modifying the mounting bracket and ensuring the cold plate covers the GPU die adequately. This is still a compromise, as VRMs and VRAM often remain air-cooled unless separate heatsinks are applied.
Building and Maintaining the Liquid Loop
* Loop Order: The order of components in the loop generally doesn’t significantly impact cooling performance because heat quickly equilibrates throughout the coolant. A common order is Pump -> Radiator -> CPU/GPU(s) -> Reservoir -> Pump. The key is to ensure the reservoir is positioned before the pump intake to ensure constant fluid supply and simplify filling/bleeding.
* Installation and Tubing Runs: Plan your tubing runs carefully to minimize sharp bends and maintain a clean aesthetic. For rigid tubing, precise measurements and careful heating (for PETG) are required.
* Filling and Bleeding: Fill the reservoir slowly with coolant. Turn on the pump in short bursts (jumping PSU pins if not connected to a PC) to circulate the fluid and remove air bubbles. Tilt the rig gently in different directions to dislodge trapped air. This process can take several hours, even overnight, for all bubbles to settle.
* Leak Testing: Crucial step. Before powering on any electronics, perform an air pressure test with a specialized leak tester, or run the pump with only the PSU connected (no mining hardware powered on) for 24 hours, placing paper towels under all fittings to detect any drips.
* Maintenance: Regular inspection for leaks, coolant level checks, and flushing/refilling the coolant (typically every 1-2 years) are essential for long-term reliability. Monitoring coolant temperature with inline sensors is also a good practice.
DIY Immersion Cooling Systems
Immersion cooling represents the pinnacle of DIY thermal management for mining, offering unparalleled heat dissipation, significantly reduced noise, and extended hardware lifespan. It involves submerging hardware directly into a non-conductive dielectric fluid, which then efficiently transfers heat away.
Understanding Dielectric Fluids
The core of immersion cooling is the dielectric fluid, which must be electrically non-conductive and have high thermal conductivity.
* Mineral Oil: The most common and budget-friendly option for DIYers. It’s readily available, non-toxic, and relatively safe to handle. However, it’s viscous, can be messy, and some plastics and rubbers (especially in cables) can degrade over time when exposed to it. It also tends to retain heat within the fluid itself, requiring effective circulation and external cooling.
* Engineered Fluids (e.g., 3M Novec, Fluorinert, BitCool): These are purpose-built, highly efficient dielectric fluids with superior thermal properties, lower viscosity, and typically no adverse effects on hardware plastics. They are often evaporative, meaning they cool by boiling and then condensing on a cooler surface (two-phase cooling), or single-phase with excellent heat transfer. The major drawback is their significantly higher cost (often thousands of dollars for a tank fill) and specialized handling requirements, making them less common for smaller DIY projects.
* Properties to Consider:
* Dielectric Strength: Ability to resist electrical breakdown. Higher is better.
* Thermal Conductivity: How well it transfers heat. Higher is better.
* Viscosity: Resistance to flow. Lower is better for easier pumping and flow.
* Boiling Point (for 2-phase fluids): Should be below the hardware’s critical temperature.
* Compatibility: Check for material compatibility with various plastics, rubbers, and sealants used in hardware.
Building a DIY Immersion Tank
The tank is the primary vessel for your submerged hardware. Its design and material are crucial for safety and functionality.
* Materials:
* Acrylic/Plexiglass: Clear, allowing visual inspection of hardware. Easy to cut and bond. Requires careful sealing (solvent welding or silicone) and structural reinforcement for larger tanks due to the fluid’s weight (mineral oil is roughly 0.8-0.9 kg/L). Thickness of 10mm or more is often recommended for larger tanks.
* HDPE (High-Density Polyethylene): Opaque, but very chemical resistant, durable, and easy to weld or fuse. Excellent for long-term durability. Less aesthetic than acrylic.
* Metal (Stainless Steel/Aluminum): Highly durable and conductive, making heat transfer to external surfaces easier. However, welding or fabricating metal requires specialized tools and skills. Must be non-reactive with the chosen fluid.
* Commercial Off-the-Shelf Containers: Large plastic storage bins or repurposed aquariums can serve as tanks for smaller, experimental setups, but often lack robust sealing or appropriate ports for plumbing.
* Sealing: Critical to prevent leaks.
* For acrylic, solvent welding creates a molecular bond. Silicone sealant (aquarium-safe, 100% silicone) can provide secondary seals or be used for HDPE.
* Consider gaskets and bulkheads for any penetrations (cables, pipes).
* Size and Design:
* The tank must be large enough to fully submerge all hardware with sufficient clearance for fluid circulation.
* Include a lid for dust prevention and to minimize evaporation (especially with engineered fluids).
* Integrate bulkheads or sealed pass-throughs for power cables, network cables, and any external pump or heat exchanger connections.
* A false bottom or stand for hardware can ensure components are fully submerged and allow for easy fluid circulation beneath them.
* Volume calculation: Measure the volume of your hardware, then add sufficient fluid volume to cover it completely with several inches of overhead. For example, a single GPU typically displaces about 1-2 liters, an ASIC significantly more.
* Safety Considerations:
* Weight: Dielectric fluids are heavy. Ensure your tank and its support structure can safely bear the full weight of the fluid and hardware. A 200-liter tank filled with mineral oil can weigh over 180 kg.
* Fire Safety: While dielectric fluids are typically non-flammable or have very high flashpoints, always exercise caution. Have appropriate fire extinguishers (Class K for cooking oils, or CO2 for electrical) nearby.
* Spill Containment: Plan for potential spills during filling or maintenance. Work over a protective liner or in an area with a floor drain.
Pump and Heat Exchange Mechanisms for Immersion
Once the hardware is submerged, the heated fluid needs to be circulated and cooled.
* Pump Selection:
* Submersible Pumps: Simple to integrate directly into the tank. Must be compatible with the dielectric fluid (many standard fountain pumps or aquarium pumps are not). Look for pumps designed for oil or chemical transfer.
* External Pumps: Often preferred for larger setups, allowing for easier maintenance and potentially more powerful options. Requires sealed tubing penetrations through the tank wall.
* Heat Exchange:
* Radiators (Air-Cooled): The most common DIY method. Fluid is pumped out of the tank, through one or more large radiators (like those used in liquid cooling, or even repurposed car radiators), and back into the tank. Fans blow air through the radiators to dissipate heat. This is effectively an external liquid-to-air heat exchanger.
* Plate Heat Exchangers (Liquid-to-Liquid): For more advanced setups, or if you want to use the waste heat, a plate heat exchanger can transfer heat from the dielectric fluid to a secondary water loop. This water loop can then be sent to an outdoor dry cooler, a chiller, or used for heat recovery (e.g., heating domestic hot water). This is significantly more complex but offers greater flexibility.
* Chillers: For extremely high heat loads or very low target temperatures, a dedicated chiller unit can be integrated into the loop to actively cool the dielectric fluid. This is typically an industrial-grade solution and quite expensive.
* Dry Coolers: Large outdoor radiators designed for continuous fluid cooling. Ideal for larger mining farms using secondary liquid loops.
Fluid Maintenance and Filtration
Maintaining the dielectric fluid’s purity is essential for long-term system health.
* Filtration: Over time, dust, debris, and even tiny metal particles can accumulate in the fluid. Integrating a fluid filter (e.g., a simple inline particulate filter for water, or a specialized oil filter) into the pump loop can extend fluid life and protect hardware.
* Fluid Replacement: While engineered fluids are designed for very long lifespans, mineral oil may degrade over several years or become contaminated, requiring replacement. Monitoring clarity and thermal performance can indicate when a fluid change is needed.
* Degassing: Especially during initial fill, air bubbles can get trapped. Running the system with the lid off for some time, or using a vacuum pump, can help degas the fluid and improve thermal contact.
Pros and Cons of Immersion Cooling for Home Miners
Aspect | Pros of DIY Immersion Cooling | Cons of DIY Immersion Cooling |
---|---|---|
Cooling Performance | Superior heat dissipation, even temperature distribution across components. Reduces throttling. | Requires careful selection and large volumes of specialized dielectric fluid. |
Noise Levels | Virtually silent operation as component fans are removed or submerged. | External cooling components (radiator fans, chillers) may still produce noise. |
Hardware Lifespan | Extended component life due to stable, low temperatures and elimination of dust/humidity. | Fluid compatibility issues can degrade certain plastics or rubbers over time. |
Dust & Humidity | Completely eliminates issues with dust buildup and humidity on sensitive electronics. | Risk of fluid leaks, mess during maintenance. |
Complexity & Cost | Scalable for high-density setups. | High initial setup cost (fluid, tank, external cooling). Significant DIY effort. |
Maintenance | Less frequent cleaning of internal components. | Fluid monitoring and occasional replacement required. Messy component removal. |
Space Efficiency | Allows for higher density packing of hardware. | Tank itself can be large and heavy. |
Environmental Controls and Enclosures
The enclosure housing your mining hardware is not just a protective shell; it’s an integral part of your cooling strategy. Proper design and environmental control within this space are crucial for maximizing the efficiency of your chosen cooling method and ensuring the longevity of your equipment.
Building a Dedicated Mining Enclosure
Whether it’s a simple box or a sophisticated server rack, the enclosure’s design impacts airflow, noise, and environmental stability.
* Material Considerations:
* Wood (Plywood, MDF): Economical, easy to work with, and offers some sound dampening. Requires careful sealing for dust control and fire resistance (consider fire-retardant paint or lining).
* Sheet Metal (Aluminum, Steel): Durable, non-flammable, and excellent for grounding. Can be challenging to work with without specialized tools. Offers good EMI shielding.
* Acoustic Foam/Panels: Lining the interior of the enclosure with sound-absorbing materials (e.g., mass-loaded vinyl, convoluted foam) can significantly reduce noise levels, a major concern for home miners. Aim for materials rated for high noise reduction coefficient (NRC).
* Ventilation Design:
* Properly sized intake and exhaust ports are critical. For air cooling, larger ports with filters are generally better.
* Consider the ‘chimney effect’ for natural convection, where cooler air enters low and hot air exhausts high.
* For forced air systems, design plenums or ducts within the enclosure to guide airflow over specific components.
* Cable Management: Beyond aesthetics, good cable management within the enclosure prevents airflow obstructions, reduces electromagnetic interference, and simplifies maintenance. Use cable ties, wire looms, or cable trays.
* Modular Design: If building a large enclosure, consider a modular design that allows for easy addition or removal of hardware, as well as simplified maintenance access. Hinged doors, removable panels, and slide-out trays can greatly improve usability.
Ventilation Design for Grow Tents and Server Racks
Many DIY miners repurpose grow tents or standard server racks as mining enclosures due to their existing ventilation infrastructure and structural integrity.
* Grow Tents:
* Pros: Inexpensive, ready-made with intake/exhaust ports, light-proof, often lined with reflective material (though not for heat).
* Ventilation: Use powerful inline duct fans for exhaust and passive (or fan-assisted) filtered intake. A 6-inch (150mm) or 8-inch (200mm) inline fan is often sufficient for a small to medium tent, capable of 400-700 CFM, ensuring multiple air changes per minute.
* Ducting: Connect exhaust fans to external vents or a cooler space using flexible aluminum ducting. Ensure the ducting is as straight and short as possible to minimize airflow resistance.
* Air Filters: Place filters on all intake ports to prevent dust. Carbon filters can also be used on exhaust to neutralize any odors if present, but they add significant airflow restriction.
* Server Racks:
* Pros: Designed for high-density equipment, excellent cable management, often have perforated doors for airflow.
* Ventilation: Can be configured for hot aisle/cold aisle containment. Rear exhaust fans (rack-mount fans) can pull hot air directly out, while front-mounted fans provide cool intake.
* Blanking Panels: Crucial for server racks. Unused U-space should be filled with blanking panels to prevent hot exhaust air from recirculating to the front intake, ensuring that all cool air is effectively directed through the equipment.
* Dedicated Rack Cooling Units: For very high-density racks, consider rack-mounted air conditioning or heat exchange units that directly integrate with the rack’s airflow path.
Controlling Humidity and Dust
Beyond cooling, managing humidity and dust is vital for electronics’ longevity.
* Humidity: High humidity accelerates corrosion and can lead to electrical shorts.
* Dehumidifiers: Essential in humid climates, especially if using evaporative coolers. Maintain humidity levels between 40-60%.
* Monitoring: Use a hygrometer (humidity sensor) to continuously monitor the environment within the enclosure.
* Vapor Barriers: In some very humid environments, sealing the enclosure with a vapor barrier can prevent moisture ingress.
* Dust: As discussed, dust is an insulator and can lead to fan failures.
* Filtration: Multi-stage filtration at all air intakes. A coarse pre-filter followed by a finer pleated filter (MERV 8-11 rating is good for general dust).
* Positive Pressure: Maintaining slightly positive pressure inside the enclosure can help prevent unfiltered air and dust from sneaking in through gaps.
* Regular Cleaning: Even with filters, periodic cleaning of internal components with compressed air or a low-pressure air blower is necessary.
Noise Reduction Strategies Integrated with Cooling
Mining rigs can be incredibly loud. Integrating noise reduction into your cooling design from the outset is far more effective than trying to dampen it post-factum.
* Fan Selection: As mentioned, larger, slower-spinning fans (120mm, 140mm) with quality bearings are quieter. Prioritize fans with lower dBA ratings.
* Fan Speed Control: PWM control allows fans to spin only as fast as necessary, reducing noise during periods of lower load or cooler ambient temperatures.
* Enclosure Insulation: Line enclosure walls with sound-absorbing materials. Mass-loaded vinyl is particularly effective at blocking sound transmission, while acoustic foam absorbs sound reflections within the enclosure.
* Vibration Isolation: Fans, pumps, and even the rigs themselves can transmit vibrations that become audible noise. Use rubber grommets, anti-vibration mounts, or spring-loaded feet for fans and other vibrating components. Placing rigs on rubber mats can also help.
* Duct Silencers: For powerful exhaust systems using inline duct fans, a duct silencer (acoustic ducting) can significantly reduce noise transmitted through the ventilation system.
* Separation: If space allows, physically separating the mining operation from living areas (e.g., in a well-insulated shed, garage, or dedicated server room) is the most effective noise reduction strategy.
DIY Heat Recovery Systems
Waste heat from mining operations can be a valuable resource, especially in colder climates. Harnessing this heat can offset heating costs, improving the overall economic efficiency of your mining venture.
* Air-to-Air Heat Recovery:
* Space Heating: The simplest method. Duct hot exhaust air from the mining enclosure directly into a living space during colder months. This works best with air-cooled setups. A 1000W mining rig can produce approximately 3412 BTUs/hour of heat, equivalent to a small space heater.
* Warm Air Distribution: Use an inline duct booster fan to push the warm air through existing HVAC ductwork or dedicated vents to distribute it evenly.
* Liquid-to-Liquid Heat Recovery (with Immersion or Liquid Cooling):
* This is where advanced heat recovery becomes highly efficient. If you are using liquid cooling or immersion cooling, the heated coolant can be routed through a secondary heat exchanger.
* Domestic Hot Water Pre-heating: Pass the heated secondary water loop (from the plate heat exchanger for the dielectric fluid) through a coil inside your domestic hot water tank. This pre-heats the water before it enters your water heater, significantly reducing its energy consumption. A well-designed system can pre-heat water by 10-20 degrees Celsius, saving a household hundreds annually on hot water bills.
* Radiant Floor Heating: The heated water can also be circulated through radiant floor heating loops, providing efficient space heating.
* Pool/Spa Heating: For larger operations, the waste heat can be effectively used to heat a swimming pool or spa. This requires a much larger heat exchanger and dedicated plumbing.
Monitoring and Automation for Optimal Cooling
Effective cooling isn’t a set-it-and-forget-it task. Continuous monitoring and automated responses are crucial for maintaining optimal temperatures, preventing issues, and maximizing efficiency.
Temperature Sensors and Their Placement
Accurate temperature data is the foundation of any smart cooling system.
* Types of Sensors:
* Thermistors: Common, inexpensive, and accurate for ambient air and liquid temperature monitoring. NTC (Negative Temperature Coefficient) thermistors are widely used.
* Thermocouples: More robust, can measure higher temperatures, often used for surface temperature of components (e.g., directly on a heatsink or power delivery module).
* Digital Sensors (e.g., DHT11/22, DS18B20): Integrated sensors that provide digital temperature and humidity readings, easy to interface with microcontrollers.
* Strategic Placement:
* GPU/ASIC Core & Memory Junction Temperatures: These are the most critical, usually read via software (e.g., HWInfo for GPUs, specific miner software for ASICs). Aim to keep GPU core temps below 65-70°C and memory junction temps below 85-90°C under load for optimal longevity. ASICs generally operate hotter, with typical temps around 70-80°C for the hashboards.
* Intake Air Temperature: Measure the temperature of the air entering your enclosure or individual rigs. This sets the baseline for your cooling potential.
* Exhaust Air Temperature: Measure the temperature of air leaving the enclosure. The delta between intake and exhaust indicates cooling efficiency. A large delta (e.g., 15-20°C) means efficient heat extraction, but also implies very hot exhaust.
* Liquid Coolant Temperature: For liquid-cooled systems, an inline temperature sensor measures the coolant temperature, directly reflecting the overall heat load. Target coolant temperatures typically range from 30-45°C.
* Ambient Room Temperature/Humidity: Crucial for overall environmental control.
DIY Fan Controllers and Automation
Microcontrollers like Arduino or Raspberry Pi offer immense flexibility for building custom, intelligent fan control systems.
* Arduino-Based Controllers:
* Hardware: Arduino Uno/Mega, temperature sensors (DS18B20 for digital, thermistors with pull-up resistors), MOSFETs or fan driver boards (e.g., PCA9685 PWM driver) to control multiple PWM fans, LCD display for local monitoring.
* Programming: Write a simple sketch (program) that reads temperature sensor data. Based on predefined temperature thresholds, the Arduino adjusts the PWM signal sent to the fan driver board, controlling fan speed. For example, if a GPU hits 60°C, fans might ramp up to 70%; at 70°C, they go to 100%.
* Benefits: Highly reliable, low power consumption, cost-effective.
* Raspberry Pi-Based Controllers:
* Hardware: Raspberry Pi (any model with GPIO pins), temperature sensors, fan controller HATs (Hardware Attached on Top) or external fan drivers.
* Programming: More powerful than Arduino, allowing for more complex logic using Python scripts. Can log data to files, send alerts via email/SMS, integrate with web interfaces for remote monitoring (e.g., using Flask or Node-RED).
* Benefits: Greater flexibility, network connectivity, easier data logging and remote access. Can integrate with existing mining software APIs.
* Integration with Mining Software: Some mining software (e.g., HiveOS, NiceHash OS) offer built-in fan control based on GPU temperatures. While basic, they are a good starting point. DIY controllers offer more granular control and can react to non-GPU temperatures (ambient, liquid).
Remote Monitoring Solutions and Alert Systems
Being able to monitor your setup from anywhere and receive timely alerts is invaluable.
* Cloud-Based Monitoring: Services like Home Assistant, Grafana (with Prometheus or InfluxDB), or simple custom web servers running on a Raspberry Pi can collect data from your sensors, visualize it on dashboards, and make it accessible remotely.
* Email/SMS Alerts: Configure your monitoring system to send automatic alerts (e.g., via Twilio for SMS, or a simple email client) if temperatures exceed critical thresholds, or if a fan fails. This proactive alerting can prevent costly hardware damage.
* Smart Plugs and Relays: Integrate smart plugs (Wi-Fi controlled outlets) or IoT relays into your system. In case of a severe overheating event or a fan failure, your automation system can trigger a smart plug to remotely shut down the power to your rig, acting as an emergency failsafe.
Safety Considerations in DIY Cooling Projects
Undertaking DIY cooling solutions, especially those involving electricity and liquids, requires a rigorous approach to safety. Overlooking these aspects can lead to equipment damage, fire hazards, or personal injury.
Electrical Safety
The high power draw of mining rigs already poses electrical risks; adding complex cooling systems necessitates even greater caution.
* Proper Wiring and Circuit Load:
* Ensure all wiring (especially for pumps and external fans) is appropriately gauged for the current it will carry. Undersized wires can overheat and cause fires.
* Do not overload electrical circuits. A typical 15-amp household circuit can safely deliver about 1440 watts. A single high-end mining rig can exceed this. Distribute rigs across multiple dedicated circuits, or install new dedicated 20-amp or 30-amp circuits as needed, professionally wired.
* Use high-quality, certified power strips and surge protectors. Avoid cheap, unrated extension cords.
* Grounding: Ensure all metal enclosures and liquid cooling components (radiators, pump housings) are properly grounded to prevent electrical shock in case of a fault.
* Circuit Breakers: Never bypass or disable circuit breakers. They are crucial safety devices designed to trip and cut power in case of an overload or short circuit.
* Water and Electricity: The most critical rule. Ensure all electrical connections are completely isolated from any potential liquid spills or condensation. Use waterproof enclosures for electrical components near liquid systems.
* Cable Management and Strain Relief: Properly route and secure all power cables to prevent kinks, chafing, and accidental disconnection. Use strain relief where cables enter enclosures.
Fire Hazards
Heat, electricity, and sometimes flammable materials (plastics, some coolants) create a potential fire risk.
* Flammable Materials: While mineral oil has a high flash point (typically >160°C or 320°F), it can still burn. Other plastics used in DIY construction might be flammable. Choose fire-retardant materials where possible.
* Overheating Components: Poor cooling can lead to components overheating to the point of ignition. This is why robust cooling and monitoring are paramount.
* Electrical Shorts: Faulty wiring, frayed cables, or liquid leaks onto electrical components can cause short circuits and arc flashes, potentially leading to fires.
* Fire Suppression: For larger DIY setups, consider placing fire extinguishers (CO2 or Class K for oil fires) nearby. Automated fire suppression systems (e.g., small server room fire suppression units) can be a significant investment but offer peace of mind.
Handling of Specialized Coolants
While most DIY-friendly coolants are relatively safe, proper handling is still necessary.
* Mineral Oil: Non-toxic, but can be messy and hard to clean up. Use gloves and eye protection. Dispose of used mineral oil responsibly according to local regulations (often treated like used motor oil).
* Engineered Fluids: While generally safe, some may require specific ventilation or handling procedures, especially during large spills. Always refer to the manufacturer’s Safety Data Sheet (SDS) for detailed instructions.
* Corrosion Inhibitors/Biocides: Pre-mixed coolants often contain these, which can be irritants. Avoid skin and eye contact.
Structural Integrity of DIY Setups
The weight of hardware and especially liquid-filled tanks can be substantial.
* Weight Distribution: Ensure the floor or surface supporting your mining setup can handle the cumulative weight. A large immersion tank can weigh hundreds of kilograms.
* Stability: Enclosures and stands must be stable and level to prevent tipping or collapse. Secure tall racks to a wall or floor.
* Sealing: For liquid systems, meticulously ensure all seals are leak-proof. A single persistent drip can lead to significant damage over time.
Cost-Benefit Analysis of DIY Cooling
Before embarking on a complex DIY cooling project, a thorough cost-benefit analysis is essential to ensure it aligns with your overall mining profitability goals.
* Initial Investment:
* Air Cooling Enhancements: High-quality fans, custom ducting materials, filters, sound insulation, temperature sensors, and microcontrollers for automation typically range from $100 to $500 for a medium-sized rig or small farm.
* Liquid Cooling (Open Loop): Water blocks, pumps, radiators, reservoirs, tubing, fittings, and coolant can easily cost $500 to $1500+ per rig, especially if cooling multiple GPUs.
* Immersion Cooling: Tank materials, fluid (especially engineered fluids), external heat exchangers, pumps, and plumbing can range from $1,000 to $5,000+ for a significant setup.
* Operational Costs:
* Power Consumption of Cooling Components: High-CFM fans, powerful pumps, and chillers consume electricity. While efficient cooling reduces rig throttling, these components add to your power bill. An optimized DIY air cooling setup can reduce the overall cooling power consumption by 15-20% compared to a poorly ventilated system running inefficient stock fans at full speed.
* Maintenance: Cost of replacement filters, thermal paste, and coolant refills.
* Benefits (Monetized):
* Increased Hash Rate/Profitability: Preventing throttling means higher sustained hash rates, directly increasing revenue. A 5% increase in hash rate due to stable temperatures can translate to significant monthly earnings for a large farm.
* Extended Hardware Lifespan: Reduced temperatures can extend hardware life by years, delaying costly replacement cycles. If a GPU costing $5000 lasts 2 years instead of 1.5, that’s a direct saving of $5000 / 3 years * 0.5 year = ~$833 in depreciation avoided.
* Reduced Power Consumption (from rig): When components run cooler, they often operate more efficiently, slightly reducing their core power draw. This is often less significant than the gain from preventing throttling.
* Lower Noise Emissions: While not directly monetized, reduced noise improves the quality of life, especially for home miners.
* Heat Recovery Savings: Monetize the value of waste heat used for home heating, hot water, or pool heating. If 2000W of waste heat is recovered for 6 months a year, that’s approximately 8760 kWh * 0.5 * $0.15/kWh = ~$657 in energy offset annually.
Calculate the Return on Investment (ROI) for your DIY cooling project. Compare the total cost of implementation against the projected savings and increased revenue over time. For many home miners, the primary benefits might be hardware longevity and noise reduction, alongside preventing immediate profitability losses from throttling.
Troubleshooting Common DIY Cooling Issues
Even with careful planning, issues can arise. Knowing how to diagnose and rectify common cooling problems is essential.
* High Component Temperatures (GPU/ASIC Hot Spots):
* Diagnosis: Check individual sensor readings. Isolate the hottest component.
* Troubleshooting Steps:
* Air Cooling: Inspect airflow path – are fans running? Are they oriented correctly (intake/exhaust)? Are there obstructions (cables, dust)? Is the intake air too warm? Is the heatsink clogged with dust? Is thermal paste/pads dry or improperly applied? (Re-apply TIM).
* Liquid Cooling: Is the pump running? Is coolant flowing? Is the radiator clean and are its fans spinning? Are there air bubbles trapped in the water block? Is the water block making good contact with the component? (Bleed loop, re-mount block).
* Immersion Cooling: Is the fluid pump running? Is the external heat exchanger working? Is the fluid level sufficient? Is the fluid contaminated or has it degraded?
* Excessive Noise:
* Diagnosis: Pinpoint the source of the noise (specific fan, pump vibration, air turbulence).
* Troubleshooting Steps:
* Fans: Check for loose fan blades, worn bearings (wobbling, grinding noise), or obstructions. Balance fan speeds with cooling needs (PWM control). Add anti-vibration mounts.
* Pumps: Listen for cavitation (gurgling, rattling from trapped air). Bleed the loop thoroughly. Ensure pump is mounted on anti-vibration pads.
* Airflow: Smooth out sharp edges in ducts, reduce fan speed if it’s creating excessive turbulence.
* Leaks in Liquid/Immersion Systems:
* Diagnosis: Visual inspection, look for coolant residue, check fluid levels frequently.
* Troubleshooting Steps: Power down immediately. Locate the leak.
* Fittings: Tighten compression fittings carefully. For barbed fittings, replace hose clamps or re-seat tubing.
* Tubing: Inspect for cracks, punctures, or signs of material degradation. Replace damaged sections.
* Components: Check water blocks and radiators for hairline cracks or manufacturing defects.
* Seals: For immersion tanks, inspect silicone seals or welded joints for breaches. Re-seal if necessary.
* System Instability/Crashes:
* Diagnosis: Often temperature-related. Monitor temperatures during crashes. Could also be PSU issues, drivers, or software.
* Troubleshooting Steps: Ensure all temperatures are within safe operating limits. If cooling seems adequate, investigate other hardware components or software configurations.
* Power Consumption Higher Than Expected:
* Diagnosis: Use a kill-a-watt meter or smart plug with power monitoring to measure total system draw.
* Troubleshooting Steps: Are fans spinning at 100% unnecessarily? Is the AC unit or chiller running constantly? Optimize fan curves. Improve general airflow to allow fans to run slower. Check for inefficient components.
By systematically approaching troubleshooting with a clear understanding of your cooling system’s design, you can efficiently resolve issues and maintain the optimal performance of your mining operations.
In conclusion, the journey of optimizing heat dissipation for cryptocurrency mining rigs is a multifaceted endeavor, moving beyond simple fan placement to encompass sophisticated environmental controls and advanced liquid-based systems. We’ve explored the foundational principles of heat transfer, the nuanced considerations for selecting and implementing various air cooling strategies, and delved into the complexities of open-loop liquid cooling and full immersion setups. From the critical importance of balanced airflow and strategic fan selection to the innovative potential of waste heat recovery, each DIY solution offers unique advantages for managing the formidable thermal output of modern mining hardware. Effective thermal management not only safeguards your significant hardware investment by extending component longevity and preventing performance-sapping thermal throttling but also contributes directly to the operational efficiency and profitability of your mining enterprise. While the initial investment in time, research, and materials for advanced DIY solutions might seem substantial, the long-term benefits in terms of sustained hash rates, reduced power consumption, and quieter operation often yield a compelling return. As mining continues to evolve, embracing these comprehensive and thoughtful approaches to cooling will remain an indispensable aspect of any successful and sustainable mining operation.
Frequently Asked Questions
How much can DIY cooling improve my mining rig’s performance?
The improvement can vary significantly. For a poorly cooled rig experiencing thermal throttling, effective DIY air cooling can lead to a 5-15% increase in stable hash rate by preventing clock speed reductions. Advanced liquid or immersion cooling can further reduce temperatures by 10-20°C compared to optimized air cooling, potentially extending hardware lifespan by 20-30% and allowing for higher overclocks, which in turn can boost hash rate by another 3-7% depending on the hardware and coin.
Is immersion cooling suitable for a small home mining setup?
While more complex and requiring a higher initial investment than air cooling, DIY immersion cooling can be suitable for a small home setup if noise reduction and maximum hardware longevity are primary concerns. A small tank for 1-2 ASICs or 4-6 GPUs is achievable, but the cost of the dielectric fluid and external heat exchanger still needs careful consideration against the benefits for such a scale.
What are the biggest risks of DIY liquid or immersion cooling?
The biggest risks are leaks causing electrical shorts and catastrophic hardware failure, and improper handling of electrical components leading to fire hazards or personal injury. Other risks include using incompatible fluids that degrade hardware materials over time, or insufficient cooling capacity from undersized heat exchangers leading to overheating despite the liquid system. Thorough leak testing and adherence to electrical safety standards are paramount.
How often should I clean my air-cooled mining rig?
The frequency depends heavily on the dustiness of your environment. In a typical home environment, cleaning dust filters every 1-2 weeks and internally dusting components every 1-2 months is a good general guideline. In very dusty conditions (e.g., garage, workshop), daily filter checks and more frequent internal cleaning might be necessary. Consistent cleaning prevents dust buildup, which insulates components and hinders airflow.
Can I use car radiator fluid in my liquid cooling loop?
No, you should never use car radiator fluid (antifreeze) in a PC or miner liquid cooling loop. Automotive coolants contain silicates and other additives designed for engine blocks and can corrode computer-grade copper or nickel water blocks, clog micro-fins, and damage pumps due to their chemical composition. Always use coolants specifically designed for computer liquid cooling systems, which contain appropriate corrosion inhibitors and biocides for electronic components.
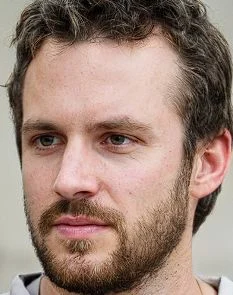
Tyler Matthews, known as “Crypto Cowboy,” is the newest voice at cryptovista360.com. With a solid finance background and a passion for technology, he has navigated the crypto world for over a decade. His writing simplifies complex blockchain trends with dry American humor. When not analyzing markets, he rides motorcycles, seeks great coffee, and crafts clever puns. Join Crypto Cowboy for sharp, down-to-earth crypto insights.