The intricacies of the modern global supply chain have evolved into a labyrinth of interconnected entities, diverse geographies, and dynamic processes. While this complexity has enabled unprecedented efficiency and access to markets, it has simultaneously introduced profound challenges, chief among them being a pervasive deficit of trust. For manufacturers, operating at the nexus of raw material procurement and finished product distribution, this erosion of confidence manifests in myriad forms: opaque sourcing practices, the insidious threat of counterfeit components, protracted dispute resolutions, and an overwhelming struggle to ensure end-to-end product integrity. This article delves into the critical imperative of fostering an environment of verifiable trust within supply chains and chronicles the transformative journey of a forward-thinking manufacturer, Opti-Flow Manufacturing Solutions, as it strategically embraced blockchain technology to forge a new paradigm of transparency and reliability.
Understanding the Crisis of Trust in Global Supply Chains
The conventional model of supply chain management, often characterized by fragmented data, disparate systems, and reliance on bilateral agreements, is inherently susceptible to vulnerabilities that undermine trust. Imagine a scenario where a critical component, sourced from a third-tier supplier in a distant country, fails unexpectedly. Pinpointing the exact origin of the defect, verifying the authenticity of its materials, or even confirming its manufacturing conditions becomes a monumental task. This lack of granular visibility and immutable record-keeping breeds an environment ripe for inefficiencies, ethical compromises, and financial losses.
The challenges are multifaceted. Firstly, there is the issue of data silos and fragmentation. Each participant in the supply chain – from raw material extractors to logistics providers, component manufacturers, and distributors – typically operates within its own proprietary systems. Data, if shared at all, often travels through insecure channels, is prone to manual error, or is selectively disclosed. This fractured information flow makes it exceedingly difficult to construct a comprehensive, verifiable narrative of a product’s journey. For a company like Opti-Flow, a global leader in precision industrial components for sectors like aerospace and automotive, this meant that while they meticulously tracked their own internal production, the provenance of specialized alloys or sub-assemblies often remained shrouded in ambiguity, relying solely on supplier declarations.
Secondly, counterfeiting and intellectual property infringement pose a significant threat. The global trade in counterfeit goods is a multi-billion-dollar industry, not only eroding legitimate sales and brand reputation but also introducing dangerous and substandard products into critical applications. In the aerospace sector, for instance, a fake bolt or a subpar hydraulic valve can have catastrophic consequences. Manufacturers struggle to authenticate every component, especially those supplied by numerous vendors, making it difficult to guarantee the integrity of their finished products. Opti-Flow had encountered several instances where their high-value industrial pumps, renowned for their reliability, were found to contain unauthorized, low-grade internal components, leading to premature failures and expensive warranty claims. This directly impacted their brand’s hard-earned reputation for engineering excellence and reliability.
Thirdly, the increasing demand for ethical sourcing and sustainability has placed immense pressure on manufacturers. Consumers, regulators, and investors are increasingly scrutinizing supply chains for evidence of fair labor practices, responsible environmental stewardship, and conflict-free mineral sourcing. Without verifiable, end-to-end traceability, proving compliance with these complex ethical mandates becomes an exercise in trust, often relying on self-reported data that lacks independent verification. Opti-Flow, like many industry leaders, was grappling with the challenge of providing irrefutable proof that their rare earth magnets and specialized metals were sourced without contributing to human rights abuses or environmental degradation. Their manual audit processes were time-consuming, expensive, and often failed to provide the necessary granular detail or real-time assurance.
Finally, the cumulative effect of these challenges leads to operational inefficiencies and financial strain. Disputes over quality, delivery timelines, or material specifications are common, leading to lengthy resolution processes that consume valuable resources and strain business relationships. Product recalls become more complex and costly without precise traceability, often requiring the recall of entire batches when only a small subset is affected. These inefficiencies directly impact profitability and a manufacturer’s ability to respond agilely to market demands or unforeseen disruptions. For Opti-Flow, the average time to resolve a quality dispute with a Tier-2 supplier could stretch for weeks, involving multiple rounds of documentation exchange, lab testing, and negotiation, often resulting in significant financial write-offs or delays in production.
It became clear to the executive leadership at Opti-Flow Manufacturing Solutions that relying on traditional, siloed systems and manual verification processes was no longer sustainable. The imperative was not just to improve efficiency but to fundamentally rebuild trust across their intricate supply network, ensuring authenticity, transparency, and accountability at every single touchpoint. They recognized that this would require a transformative technological solution capable of providing an immutable, shared record of information, accessible to all authorized parties. Their exploration led them inevitably to blockchain.
Blockchain as a Foundational Technology for Supply Chain Trust
At its core, blockchain technology offers a decentralized, distributed, and immutable ledger system that records transactions across a network of computers. Unlike a traditional database where a single entity holds central control, a blockchain’s data is shared and synchronized across all participating nodes. Once a transaction – or block of data – is added to the chain, it is cryptographically linked to the previous block, creating a permanent, tamper-proof record. This inherent design provides the foundational elements necessary to address the trust deficiencies prevalent in complex supply chains.
The distinctive attributes of blockchain directly tackle the core problems faced by manufacturers like Opti-Flow.
- Transparency and Shared Visibility: In a permissioned blockchain (which is typically used in enterprise supply chain applications), authorized participants gain access to a shared, real-time view of data relevant to them. This means that when a raw material supplier logs a shipment, or a quality control check is performed at a sub-component manufacturer’s facility, that data is recorded on the ledger and becomes visible to Opti-Flow and other authorized parties almost instantly. This eliminates information asymmetry and allows for proactive issue identification rather than reactive problem-solving. It’s about creating a single source of truth, eliminating the need for constant reconciliation of disparate records.
- Immutability and Data Integrity: The cryptographic linking of blocks ensures that once data is recorded on the blockchain, it cannot be altered or deleted. Any attempt to tamper with a record would break the chain and be immediately apparent to all network participants. This immutability is crucial for establishing an unquestionable audit trail. For Opti-Flow, this meant that material certifications, production dates, and quality inspection results were permanently logged, providing indisputable proof of origin and compliance. This significantly reduces the potential for fraud, misrepresentation, or data manipulation throughout the product’s lifecycle.
- Traceability and Provenance: By recording every significant event in a product’s journey – from the source of raw materials to manufacturing steps, packaging, and distribution – blockchain creates a granular, end-to-end traceability map. Each event is a “transaction” on the ledger, linked to the unique identifier of the product or batch. This allows manufacturers to trace any component back to its original source or forward to its final destination with unprecedented speed and accuracy. In a product recall scenario, instead of recalling an entire production run, Opti-Flow could pinpoint precisely which batches or even individual items were affected, minimizing costs and customer inconvenience.
- Smart Contracts for Automation and Efficiency: Smart contracts are self-executing agreements with the terms of the agreement directly written into lines of code. They run on the blockchain, automatically executing predefined actions when certain conditions are met. For supply chains, this translates into automated processes that eliminate manual interventions and reduce the potential for errors or delays. Examples include automatic release of payment to a supplier once a shipment is verified as delivered and meeting quality specifications, or the automatic initiation of a compliance audit if a specific supplier’s certification expires. This capability dramatically streamlines operations, reduces administrative overhead, and enforces contractual obligations without human intervention.
- Enhanced Security and Resilience: The decentralized nature of blockchain means there is no single point of failure that can be targeted by cyberattacks. The data is distributed across multiple nodes, making it highly resilient to outages and malicious activity. Cryptographic techniques protect data privacy while allowing for selective sharing, addressing concerns about competitive intelligence. This robust security framework is paramount for protecting sensitive supply chain information.
When evaluating blockchain solutions, Opti-Flow recognized that while public blockchains like Ethereum offer unparalleled decentralization, they might not be suitable for enterprise supply chains due to concerns around transaction speed, scalability, and data privacy, as business-sensitive information needs to remain confidential among competitors or specific partners. Therefore, they focused on permissioned blockchains, specifically consortium chains or private enterprise blockchains. These allow organizations to control who can participate in the network, validate transactions, and access specific data. Platforms like Hyperledger Fabric, Corda, or enterprise versions of Ethereum (e.g., Quorum) provide the necessary privacy, performance, and governance capabilities required for complex business ecosystems. This choice reflected a pragmatic approach to harnessing blockchain’s benefits while addressing the unique requirements of a competitive industrial sector. Their decision was guided by the need for a solution that balanced transparency with necessary data privacy, while offering robust smart contract capabilities and high transaction throughput.
A Manufacturer’s Journey: The Genesis of Opti-Flow’s Blockchain Adoption
The decision to embark on a blockchain adoption journey was not taken lightly by Opti-Flow Manufacturing Solutions. For years, Opti-Flow had built its reputation on delivering high-precision industrial components, ranging from advanced hydraulic systems for aerospace to specialized drive train components for heavy machinery. Their sprawling global supply chain encompassed hundreds of Tier-1, Tier-2, and Tier-3 suppliers, each contributing critical materials and sub-assemblies. Despite stringent internal quality controls, the company faced mounting pressures that conventional methods struggled to alleviate.
The genesis of their blockchain initiative stemmed from a series of escalating pain points:
- Persistent Counterfeit Incursions: The most pressing issue was the alarming rise in counterfeit components entering their supply stream. These look-alike parts, often made from inferior materials or lacking proper heat treatments, led to premature product failures in the field. One particular incident involving faulty bearings in a batch of aerospace actuators resulted in an extensive recall, costing Opti-Flow upwards of $12 million in warranty claims, logistics, and reputational damage. The lack of verifiable provenance for these bearings made it nearly impossible to quickly identify the point of compromise or the responsible party.
- Opaque Raw Material Sourcing: Growing regulatory demands and customer expectations for ethical and sustainable sourcing of materials, particularly for specialized alloys and rare earth elements, presented a significant compliance burden. Opti-Flow relied on supplier declarations, which, while helpful, lacked the immutable, third-party verifiable proof customers and auditors increasingly demanded. Tracing an alloy back to a specific mine or proving its conflict-free status was a labor-intensive, often inconclusive process.
- Inefficient Quality Dispute Resolution: When quality issues arose, the process of fault identification and dispute resolution was notoriously slow. It involved exchanging stacks of paper documents, manual data entry, phone calls, and site visits across multiple time zones. This protracted back-and-forth often delayed production, tied up valuable resources, and strained relationships with long-term suppliers. The average time to resolve a significant quality dispute could be as long as six weeks.
- Limited End-to-End Visibility: Opti-Flow’s ERP system provided excellent visibility within its own four walls, but beyond that, the chain became opaque. They knew what was shipped *to* them and what was shipped *from* them, but the journey in between – conditions during transit, intermediate processing steps by sub-contractors, or changes in material origin – was largely a black box. This made proactive risk management and supply chain resilience difficult to achieve.
The executive team, led by CEO Evelyn Chen and CIO Marcus Thorne, recognized that these were not isolated problems but systemic issues requiring a fundamental shift in how supply chain data was managed and trusted. They initiated a comprehensive review of emerging technologies that could provide truly verifiable, shared data across their ecosystem. Artificial intelligence, IoT, and advanced analytics were all on the table, but it was blockchain’s unique capabilities around immutability, transparency, and smart contracts that resonated most strongly with their core need for trust and traceability.
The decision-making process involved several key steps:
- Exploratory Phase (6 months): A cross-functional task force, comprising representatives from procurement, quality assurance, IT, legal, and operations, was established. They engaged with industry analysts, attended conferences, and consulted with technology vendors specializing in blockchain for supply chains. Initial feasibility studies were conducted to assess the technical viability and potential business impact.
- Business Case Development (3 months): The task force built a compelling business case, quantifying the potential return on investment (ROI). They estimated that reducing counterfeit incidents by even 50% could save millions annually, while faster dispute resolution and improved audit efficiency offered substantial operational cost reductions. The intangible benefits, such as enhanced brand reputation and increased customer loyalty due to verifiable product authenticity, were also heavily weighted.
- Executive Buy-in and Champion Identification: Securing commitment from the highest levels of management was crucial. CIO Marcus Thorne became the internal champion, articulating the strategic imperative of digitalizing trust to the board. His ability to translate complex technical concepts into clear business advantages was pivotal in gaining the necessary financial and organizational backing. The board approved an initial investment of $2.5 million for a pilot project, recognizing it as a strategic move to future-proof their supply chain.
-
Pilot Project Scoping: To mitigate risk and demonstrate tangible value quickly, Opti-Flow decided on a focused pilot. They selected their aerospace-grade hydraulic actuator line for the initial deployment. This product line was high-value, prone to counterfeiting, and involved complex bill-of-materials with multiple critical suppliers, making it an ideal candidate to test the full spectrum of blockchain’s capabilities. The pilot would involve five key suppliers (raw material providers, specialized forging companies, and sub-component manufacturers) and two of Opti-Flow’s own assembly plants. The primary objectives were:
- Achieve end-to-end traceability of all critical components.
- Reduce the incidence of suspected counterfeit parts by at least 70% within the pilot scope.
- Streamline the quality dispute resolution process by 50%.
- Automate compliance verification for specific material certifications.
This systematic approach, combining careful research with a strategic, phased implementation plan, laid the groundwork for Opti-Flow’s successful adoption of blockchain, transforming a significant challenge into a foundational competitive advantage.
Designing the Blockchain Solution for Opti-Flow
Once the decision to proceed with a pilot project was made, the Opti-Flow team, in collaboration with their chosen technology partner, embarked on the intricate process of designing the blockchain solution. This involved critical choices regarding the underlying platform, the data architecture, integration strategies, and the definition of participant roles and smart contract logic. The goal was to build a robust, scalable, and secure system that could seamlessly integrate with Opti-Flow’s existing operational infrastructure while providing the unprecedented levels of transparency and immutability they sought.
Their selection process for the blockchain platform was rigorous. After evaluating several options, Opti-Flow opted for a Hyperledger Fabric-based solution. This choice was driven by several key factors:
- Permissioned Network: Hyperledger Fabric allows for a permissioned network, meaning only authorized participants can join and interact with the ledger. This was crucial for Opti-Flow, as it needed to share sensitive supply chain data without exposing it to competitors or the general public.
- Privacy through Channels: Fabric’s channel architecture enabled multiple participants to transact privately within specific sub-groups (channels) without exposing all data to the entire network. For example, Opti-Flow could have a channel with its raw material supplier for highly specific material composition data, while a different channel might exist for logistics and shipment information accessible to carriers and distributors.
- Smart Contract Flexibility (Chaincode): Fabric’s “chaincode” (its term for smart contracts) can be written in common programming languages like Go, Java, or Node.js, making it easier for Opti-Flow’s existing development team to learn and manage. The ability to update chaincode through consensus was also a significant advantage for iterative development.
- Scalability and Performance: Fabric is designed for enterprise-grade performance, capable of handling thousands of transactions per second, which was a critical consideration for a global manufacturer like Opti-Flow with high transaction volumes.
- Strong Governance Model: The Hyperledger project, overseen by the Linux Foundation, provided a robust governance model and a growing ecosystem of tools and support, reducing vendor lock-in risks.
The next crucial step was defining the key data points to be recorded on the blockchain. This required detailed mapping of the entire supply chain process for the hydraulic actuator product line. The team identified critical data elements that, when immutably recorded, would provide a comprehensive and verifiable digital twin of the product’s journey. These included:
- Raw Material Origin and Certifications: Chemical composition analysis, heat treatment logs, mill certificates, mine of origin data (for ethical sourcing compliance), and quality assurance reports. Each batch of raw material received a unique blockchain ID.
- Production Batches and Manufacturing Events: Timestamped records of each manufacturing step, including machine IDs, operator IDs, environmental conditions (temperature, humidity), and the output quantity. This included forging, machining, plating, and assembly stages.
- Quality Control Checkpoints: Results of all in-process and final inspection reports, including pass/fail status, measured parameters, inspection dates, and the identity of the inspector. Any non-conformances were logged here.
- Component Serial Numbers: For high-value individual components, unique serial numbers were linked to their production history and material provenance. For lower-value bulk items, batch IDs were used.
- Shipment and Logistics Details: Carrier information, departure and arrival times, shipping conditions (e.g., temperature and humidity data from IoT sensors attached to containers), customs declarations, and proof of delivery.
- Product Assembly Records: For Opti-Flow’s own assembly lines, records of which sub-components (with their unique blockchain IDs) were incorporated into which final product assembly.
- Post-Sale Maintenance and Repair History: While initially focused on pre-sale traceability, the design included the capability to log post-sale service events, enabling a full lifecycle history for each actuator.
Integration with existing systems was identified as a paramount challenge but also a critical success factor. A blockchain solution cannot operate in isolation. Opti-Flow’s legacy systems included a powerful SAP ERP for resource planning, Siemens MES (Manufacturing Execution System) on the shop floor, and various custom CRM and logistics platforms. The solution architecture called for a robust API layer to connect the blockchain network with these existing systems. For example, data from the MES (e.g., machine operation logs, QC results) was automatically pushed to the blockchain via API gateways, eliminating manual data entry. Similarly, procurement orders from the ERP could trigger smart contracts on the blockchain for supplier onboarding and initial data entry requirements.
Defining participant roles and access permissions was another key design element. The network was structured with Opti-Flow as the orchestrator, alongside its five pilot suppliers and two logistics partners. Each participant was granted specific permissions to view and add data relevant to their role, ensuring data privacy and competitive confidentiality. For instance, a raw material supplier could see only the data related to the materials they supplied, and only up to the point it left their facility, while Opti-Flow had an end-to-end view of its product’s components. Auditors and regulators could be granted temporary, read-only access to specific data streams for compliance checks, significantly streamlining their processes.
Finally, the development of smart contracts was central to automating trust and streamlining operations. Key smart contracts developed for the pilot included:
- Quality Gate Enforcement: Automatically triggered if a quality control report (logged on the blockchain) indicated a non-conformance. This would automatically flag the batch, prevent further processing, and notify the relevant teams for investigation.
- Automated Payment Release: Upon verification of a certified delivery (logged by a logistics partner and confirmed by Opti-Flow’s receiving dock) and matching quality parameters, the smart contract would initiate a payment request to the ERP system, significantly shortening payment cycles.
- Compliance Attestation: For specific material certifications (e.g., aerospace-grade titanium), suppliers would upload digital certificates, which, upon verification by the smart contract against predefined criteria, would automatically mark the material as compliant.
The comprehensive design phase, meticulously planned over four months, laid the technical and operational blueprint for Opti-Flow’s blockchain initiative, setting the stage for its subsequent implementation and phased rollout. It ensured that the technology would not merely exist as a standalone solution but would become an integral, reinforcing layer within their existing, complex manufacturing ecosystem.
Implementation and Phased Rollout at Opti-Flow
The theoretical design of Opti-Flow’s blockchain solution transitioned into tangible reality through a carefully orchestrated implementation and phased rollout strategy. Recognizing the inherent complexities of integrating a novel technology across a multi-party ecosystem, Opti-Flow adopted an agile approach, starting small, learning fast, and scaling gradually.
The Pilot Phase: Building the Foundation (6 months)
The initial pilot focused exclusively on the aerospace-grade hydraulic actuator line, involving five key suppliers and two of Opti-Flow’s internal assembly plants. This contained environment allowed the team to fine-tune the technology and processes without disrupting the entire global operation.
Key activities during the pilot included:
- Node Setup and Network Configuration: Setting up Hyperledger Fabric nodes at Opti-Flow and securely connecting the five participating suppliers’ systems. This involved significant IT effort in network configuration, security hardening, and establishing secure API endpoints for data exchange.
- System Integration and API Development: This was a monumental task. Opti-Flow’s existing SAP ERP and Siemens MES systems needed to seamlessly feed data into the blockchain and receive outputs. Custom APIs were developed for automated data ingestion from MES sensors (e.g., temperature, humidity, machine throughput) and for pushing key events (e.g., material reception, quality sign-offs) from ERP to the ledger. Initial integration challenges included differing data formats, latency issues, and ensuring data integrity during transfer.
- Supplier Onboarding and Training: This was arguably the most critical and challenging aspect. Opti-Flow invested heavily in educating its pilot suppliers. Workshops were held, clearly explaining the benefits (e.g., faster payments, reduced audit burdens, enhanced reputation for trustworthiness) and providing practical, step-by-step guides on how to input data into the new system. Initial resistance stemmed from concerns about data privacy, additional workload, and the perceived complexity of new technology. Opti-Flow addressed this by emphasizing the permissioned nature of the network, ensuring data confidentiality, and providing dedicated support teams. They even subsidized initial setup costs for smaller suppliers to alleviate financial burdens.
- Smart Contract Development and Testing: The predefined smart contracts for quality gates, payment automation, and compliance attestations were developed and rigorously tested in a sandbox environment before live deployment. Iterative feedback from legal and operations teams helped refine the contract logic.
- Data Migration and Initial Load: A crucial early step was loading historical data for the pilot product line (where available and verifiable) onto the blockchain to establish a baseline. This involved careful data cleansing and validation.
Challenges Encountered During Pilot:
- Data Input Accuracy and Discipline: Despite training, some suppliers initially struggled with consistent and accurate data entry. Opti-Flow implemented automated data validation rules and real-time alerts to flag inconsistencies, requiring immediate correction.
- Interoperability with Diverse Supplier Systems: While Opti-Flow standardized its API, suppliers used a wide array of internal systems, from advanced ERPs to simple spreadsheets. Tailored integration solutions or simplified web interfaces were sometimes necessary to accommodate less technologically mature partners.
- Legal and Contractual Framework: Crafting consortium agreements that legally bound all participants regarding data sharing, governance, and dispute resolution on the blockchain was complex and required extensive legal counsel.
Lessons Learned and Iterative Improvements:
The pilot phase yielded invaluable insights. Opti-Flow learned the importance of continuous stakeholder engagement, simplified user interfaces, and robust error handling. They discovered that a “carrot” approach, highlighting benefits like expedited payment or reduced audit frequency, was far more effective than a “stick” approach in driving supplier adoption. The initial metrics tracked provided encouraging results:
- Reduction in dispute resolution time for pilot products: 35%
- Improvement in audit efficiency for provenance: 40%
- Identification of 3 previously undetected instances of non-compliant material shipments.
Scaling Up: Expanding the Network (Ongoing)
Following the successful pilot, Opti-Flow commenced the strategic scaling of the blockchain solution across its broader supply chain. This phased expansion, planned over three years, involved bringing on more product lines, additional suppliers (both Tier-1 and deeper into Tier-2/3), and extending geographical coverage.
Strategies for Scaling:
- Standardized Onboarding Kits: Based on pilot learnings, Opti-Flow developed comprehensive onboarding kits for new suppliers, including detailed FAQs, video tutorials, and pre-configured API templates.
- Dedicated Supplier Relationship Managers: Cross-functional teams were assigned to work directly with new suppliers to guide them through the integration and training process, fostering a collaborative environment.
- Modular Rollout: Instead of a big-bang approach, new product lines or clusters of suppliers were brought onto the network incrementally, allowing for continuous optimization and risk mitigation.
- Addressing Data Governance and Legal Frameworks: As the network grew across different jurisdictions, Opti-Flow engaged legal experts to navigate varying data privacy regulations (e.g., GDPR, CCPA) and establish robust, globally compliant data governance policies within the blockchain consortium.
- Performance Monitoring and Optimization: Regular monitoring of network performance, transaction throughput, and data latency ensured the system scaled efficiently without bottlenecks. Investments in cloud infrastructure and dedicated blockchain engineers were critical.
- Internal Change Management: Employee training was extended company-wide, from procurement specialists to quality engineers and finance teams, ensuring they understood how to leverage the new data for their respective roles. Internal champions in each department helped drive adoption.
The phased rollout underscored Opti-Flow’s commitment to strategic digital transformation. It demonstrated that while the initial investment and effort were significant, a well-planned implementation journey, focused on proving value incrementally, was key to successfully building a truly trusted and transparent supply chain.
Tangible Benefits and Measurable Impact for Opti-Flow
The adoption of blockchain technology by Opti-Flow Manufacturing Solutions was not merely a technological upgrade; it represented a fundamental shift in their operational paradigm, yielding a cascade of tangible benefits and measurable impacts across their entire value chain. The investment, initially viewed as substantial, quickly proved its worth through quantifiable improvements in trust, efficiency, financial performance, and sustainability.
Enhanced Trust and Transparency
- Verifiable Authenticity and Counterfeit Reduction: The most immediate and profound impact was the dramatic reduction in counterfeit components. With every critical part traceable via a unique blockchain ID, Opti-Flow could verify the authenticity of materials and sub-assemblies in real-time. For their aerospace actuator line, counterfeit incidents dropped by an astonishing 92% within 18 months of full blockchain integration, saving an estimated $8 million annually in warranty claims and product failure investigations for this specific line. This level of traceability significantly deterred counterfeiters, as their products could no longer masquerade undetected within Opti-Flow’s authenticated supply chain.
- Unprecedented End-to-End Visibility: Opti-Flow now possessed a comprehensive, immutable digital record of every product’s journey from its raw material origins to the final customer. This meant that in the rare event of a product anomaly, they could pinpoint the exact batch, manufacturing conditions, and even the specific machine or operator involved, enabling surgical precision in problem identification and resolution. This transparency extended to customers, who, with permission, could verify the provenance of their purchased products, boosting confidence and brand loyalty.
- Improved Brand Reputation and Customer Confidence: By being able to irrefutably guarantee the authenticity and ethical sourcing of its products, Opti-Flow differentiated itself in a competitive market. New marketing campaigns centered around “Verifiably Authentic” products resonated strongly with their clients, particularly in sensitive sectors where product integrity is paramount. Customer satisfaction surveys showed a 15% increase in “trust in product quality and origin” scores post-blockchain implementation.
Operational Efficiencies
- Streamlined Dispute Resolution: The availability of immutable, shared data on the blockchain drastically reduced the time and effort required to resolve quality or delivery disputes with suppliers. No longer were discussions based on “he said, she said” or conflicting paper records. The transparent, timestamped ledger provided an indisputable source of truth. The average time to resolve quality disputes with Tier-1 and Tier-2 suppliers decreased by 75%, from an average of six weeks to just over ten days. This freed up valuable personnel and strengthened supplier relationships built on mutual transparency.
- Automated Compliance and Auditing: Smart contracts automated the verification of various certifications (e.g., ISO, environmental standards, conflict-free mineral declarations). This eliminated significant manual effort and human error. External audits, which previously took weeks of preparation and on-site verification, could now be completed in a matter of days by granting auditors secure, temporary access to relevant blockchain data. Audit readiness improved by 80%, and compliance reporting became instantaneous.
- Optimized Inventory Management: Enhanced real-time visibility into incoming materials and sub-components allowed for more precise demand forecasting and just-in-time inventory strategies, reducing holding costs and minimizing waste.
- Faster Recalls: In the event of a quality issue necessitating a product recall, the granular traceability provided by the blockchain enabled Opti-Flow to identify precisely affected batches or even individual serialized products within minutes, rather than days or weeks. This drastically reduced the scope and cost of recalls, minimizing public safety risks and reputational damage.
Financial Advantages
- Significant Cost Savings: The projected annual savings from reduced counterfeit incidents, faster dispute resolution, optimized inventory, and expedited recalls collectively amounted to an estimated $10-12 million annually across Opti-Flow’s integrated product lines once fully scaled. This far outstripped the initial investment in the blockchain solution.
- Improved Cash Flow: Smart contracts automating payment releases upon verified delivery and quality checks accelerated payment cycles for suppliers, in turn potentially allowing Opti-Flow to negotiate more favorable terms or receive discounts for prompt payment.
- Reduced Insurance Premiums: As Opti-Flow’s supply chain risk profile demonstrably lowered due to enhanced traceability and counterfeit mitigation, discussions with insurance providers began exploring potential reductions in product liability and supply chain disruption insurance premiums. While still in negotiation, initial estimates suggested a potential 5-10% reduction in certain premium categories.
Sustainability and Ethical Sourcing
- Verifiable Ethical Provenance: Opti-Flow could now provide undeniable, auditable proof of origin for its raw materials, including rare earth elements and specialized metals, demonstrating their commitment to conflict-free sourcing and responsible environmental practices. This was invaluable for meeting stringent regulatory requirements and satisfying the growing demand from socially conscious customers. In the first year of full blockchain integration, they identified and remediated 15% of supplier non-compliance issues related to sustainability certifications, directly improving their environmental and social governance (ESG) standing.
- Demonstrating Fair Labor Practices: While more complex to implement, smart contracts were being explored to link supplier attestations regarding fair labor practices to verifiable external audits, creating a more transparent and accountable framework for social responsibility within the supply chain.
The impact was transformative. Opti-Flow’s blockchain adoption journey moved them from a reactive position, constantly battling opacity and risk, to a proactive stance, where trust was an inherent, verifiable feature of their operations. This shift not only safeguarded their existing business but also unlocked new opportunities for strategic partnerships and market differentiation, proving that building trust is not just an ethical imperative but a powerful competitive advantage.
Addressing the Hurdles and Mitigating Risks in Blockchain Adoption
While the benefits of blockchain adoption were undeniably compelling for Opti-Flow, the journey was far from devoid of significant challenges. Implementing a technology that fundamentally alters how data is shared and trusted across an ecosystem requires careful navigation of technological complexities, organizational inertia, and evolving regulatory landscapes. Opti-Flow’s success hinged on its proactive approach to identifying and mitigating these hurdles.
Technological Integration Complexities
One of the most formidable challenges was integrating the new blockchain network with Opti-Flow’s existing legacy systems. Their robust SAP ERP, Siemens Manufacturing Execution System (MES), and various bespoke applications were not designed to seamlessly interact with a distributed ledger. The team had to:
- Develop Robust APIs: Building and maintaining secure, high-performance Application Programming Interfaces (APIs) to allow data flow between traditional databases and the blockchain was a continuous effort. This required deep expertise in both legacy system architecture and blockchain protocols.
- Data Harmonization: Ensuring data consistency and accuracy across disparate systems was crucial. Data cleansing, standardization, and establishing clear data ownership rules were necessary to prevent “garbage in, garbage out” scenarios on the immutable ledger.
- Infrastructure Scalability: As the network expanded and transaction volumes grew, Opti-Flow needed to ensure its underlying cloud infrastructure and blockchain nodes could handle the load without compromising performance. This involved continuous monitoring, capacity planning, and optimizing the chaincode for efficiency.
Interoperability with Diverse Partner Systems
Opti-Flow’s supply chain comprises partners with varying levels of technological maturity. While some Tier-1 suppliers had sophisticated ERP systems, many smaller Tier-2 and Tier-3 manufacturers operated with simpler setups. This led to interoperability challenges:
- Bridging Technology Gaps: For less tech-savvy suppliers, Opti-Flow developed user-friendly web portals or simplified data submission tools that abstracted away the blockchain’s complexity. For larger partners, customized API integrations were required, often needing close collaboration with the partner’s IT teams.
- Cross-Network Communication: As other industry players began exploring their own blockchain initiatives, the prospect of needing to communicate across different blockchain networks (e.g., a Hyperledger Fabric network connecting to a Corda network) emerged. Opti-Flow began researching interoperability standards and cross-chain communication protocols to prepare for a multi-blockchain future, understanding that isolated networks would limit the full potential of DLT.
Data Privacy and Confidentiality Concerns
Sharing sensitive business data on a shared ledger, even a permissioned one, raised legitimate concerns about competitive intelligence and data confidentiality. Opti-Flow addressed these through:
- Strict Access Control: Meticulously defining roles and permissions to ensure participants only saw data relevant to their specific interactions. This was central to the Hyperledger Fabric channel architecture.
- Off-Chain Storage for Sensitive Data: Large or highly proprietary files (e.g., detailed engineering blueprints, proprietary chemical formulas) were stored off-chain in encrypted databases, with only a cryptographic hash or pointer stored on the blockchain for verification.
- Zero-Knowledge Proofs (ZKPs): While still in nascent stages for their enterprise application, Opti-Flow was exploring ZKPs, which allow one party to prove that they possess certain information without revealing the information itself. This could be crucial for verifying compliance without disclosing underlying sensitive data to all network participants.
Governance and Standards
Establishing a common set of rules, protocols, and governance models for a multi-party blockchain consortium was a significant undertaking:
- Consortium Agreement: Developing a legally binding consortium agreement that covered data ownership, dispute resolution mechanisms, intellectual property rights, and the process for adding or removing participants was crucial. This required extensive legal consultation across multiple jurisdictions.
- Evolution of Standards: The blockchain space is still evolving rapidly. Opti-Flow actively participated in industry working groups to contribute to and align with emerging global standards for supply chain data models and interoperability, aiming to avoid future fragmentation.
Cost of Implementation and Maintenance
The initial investment in technology, talent, and integration for a comprehensive blockchain solution can be substantial. Opti-Flow managed this by:
- Phased Implementation: Starting with a focused pilot allowed them to demonstrate ROI incrementally, justifying further investment.
- Leveraging Open-Source Technologies: Utilizing Hyperledger Fabric, an open-source framework, helped reduce licensing costs compared to proprietary solutions. However, the cost of skilled developers and system integrators remained a significant expenditure.
- Long-Term Value Proposition: The focus was always on the long-term strategic advantage and quantifiable savings (e.g., reduced counterfeit losses, lower recall costs) that would ultimately outweigh the upfront investment.
Change Management and Human Factors
Perhaps the most underestimated challenge was overcoming organizational inertia and resistance to change. Employees and partners were accustomed to established processes, and the shift to a blockchain-enabled workflow required significant effort in:
- Education and Training: Continuous, tailored training programs for all stakeholders, from procurement teams to warehouse staff and external suppliers, explaining the “why” and “how” of the new system.
- Demonstrating Immediate Value: Highlighting how the new system directly benefited their daily work (e.g., faster payment for suppliers, less paperwork for quality control) was key to gaining adoption.
- Leadership Buy-in and Communication: Consistent communication from senior leadership about the strategic importance of the initiative helped reinforce its necessity and drive cultural acceptance.
By proactively identifying these hurdles and developing comprehensive strategies to address them, Opti-Flow not only navigated the complexities of blockchain adoption but also demonstrated resilience and adaptability, setting a precedent for other manufacturers looking to build trusted supply chains.
The Future of Trust-Based Supply Chains and Opti-Flow’s Vision
Opti-Flow Manufacturing Solutions’ journey with blockchain has clearly demonstrated that building trust into the very fabric of a supply chain is not merely aspirational but eminently achievable, yielding substantial returns. As the company looks towards the horizon, its vision extends beyond just traceability and authenticity. The established blockchain foundation is seen as a launchpad for further innovation, enabling a truly intelligent, resilient, and adaptive supply chain ecosystem. The future of trust-based supply chains, as envisioned by Opti-Flow, is characterized by deep integration, predictive capabilities, and collaborative intelligence.
Expansion and Deeper Integration
Having successfully implemented blockchain for their aerospace hydraulic actuators, Opti-Flow plans to expand the solution across other high-value and high-risk product lines, including specialized automotive components and medical device parts, over the next three to five years. This phased expansion will leverage the established governance model and technical architecture, while adapting to the unique nuances of each product’s supply chain.
- Broadening Supplier Network: The goal is to onboard an even greater proportion of their Tier-1, Tier-2, and critical Tier-3 suppliers onto the blockchain network, creating a truly comprehensive, end-to-end digital twin of their entire supply chain.
- Integrating with Customer Ecosystems: Opti-Flow is exploring ways to extend the blockchain’s reach to its end-customers, particularly large industrial clients, allowing them to verify product provenance and even track the lifecycle history (maintenance, repairs) of installed components. This could unlock new service-based business models and enhance long-term customer relationships.
- Financial Supply Chain Integration: Further integration of the blockchain with financial systems to enable more sophisticated forms of supply chain finance, such as dynamic discounting and trade finance, where the immutable records on the ledger provide real-time, verifiable data for risk assessment and transaction execution.
Synergy with Emerging Technologies
The true power of blockchain unfolds when synergistically combined with other cutting-edge technologies. Opti-Flow is actively investing in research and development to integrate their blockchain with:
-
Artificial Intelligence (AI) and Machine Learning (ML):
- Predictive Analytics for Risk Mitigation: AI algorithms, trained on the vast, verified dataset on the blockchain (e.g., historical quality issues, supplier performance, geopolitical events), can develop predictive models to identify potential supply chain disruptions or quality anomalies before they occur. For example, machine learning could detect subtle patterns in sensor data that indicate a component is likely to fail prematurely, triggering proactive maintenance or replacements.
- Demand Forecasting Optimization: AI can leverage granular, real-time demand signals from the blockchain (e.g., product sales, maintenance requests) to improve the accuracy of demand forecasting, leading to optimized production schedules and reduced inventory waste.
-
Internet of Things (IoT):
- Enhanced Real-time Monitoring: Expanding the deployment of IoT sensors on high-value components and shipments to capture even more granular, real-time data – temperature, humidity, shock, GPS location – directly onto the blockchain. This creates an even richer, verifiable data stream, crucial for sensitive products or those requiring specific environmental conditions. For instance, temperature excursions during transit could automatically trigger alerts and smart contract clauses.
- Digital Twins: Combining blockchain’s immutable record of a product’s history with IoT’s real-time performance data and AI’s predictive capabilities will enable the creation of comprehensive digital twins. These virtual replicas of physical assets will offer unparalleled insights into a product’s current state, past performance, and future potential, optimizing maintenance, usage, and end-of-life management.
- Augmented Reality (AR) and Virtual Reality (VR): Exploring the use of AR for enhanced visualization of blockchain-verified product information on the factory floor or during field service, allowing technicians to overlay digital data (e.g., component history, assembly instructions) onto physical objects.
Collaborative Ecosystems and Industry Standards
Opti-Flow envisions a future where trust extends beyond individual enterprise supply chains to broader, interconnected industry ecosystems. They are actively engaging in:
- Cross-Industry Collaboration: Working with industry bodies and other leading manufacturers to establish common data models and interoperability standards for blockchain-based supply chain solutions. This collective effort is crucial to avoid fragmented blockchain islands and create truly seamless, verifiable global trade networks.
- Multi-Party Data Sharing Frameworks: Exploring models for secure, privacy-preserving data sharing across multiple, potentially competing organizations to address grand challenges like circular economy initiatives, global carbon footprint tracking, or rapid response to pandemics, where shared, trusted data is paramount.
The Long-Term Strategic Advantage
For Opti-Flow, the blockchain initiative is not a one-off project but an ongoing strategic imperative. Being a pioneer in verifiable trust has yielded significant competitive advantages:
- Resilience and Adaptability: A transparent, data-rich, and automated supply chain is inherently more resilient to disruptions, whether from geopolitical events, natural disasters, or unexpected quality issues. Opti-Flow’s ability to quickly identify and react to anomalies gives them a critical edge in an increasingly volatile global landscape.
- Innovation and New Business Models: The trusted data foundation opens doors to innovative business models, such as “Product-as-a-Service,” where Opti-Flow sells the usage of its components rather than just the components themselves, backed by verifiable performance and maintenance histories.
- Leadership in Sustainability and Ethics: Their verifiable ethical sourcing and environmental footprint tracking capabilities position Opti-Flow as a leader in corporate social responsibility, appealing to a growing segment of discerning customers and investors.
Opti-Flow’s vision for the future is one where trust is no longer an assumption but a verifiable, data-driven certainty. Their blockchain adoption story is a testament to the transformative power of this technology, paving the way for a new era of secure, transparent, and resilient global supply chains.
In the complex and often opaque world of modern manufacturing and logistics, the imperative to build robust trust across extended supply chains has never been more pronounced. The conventional reliance on fragmented data systems, manual verification, and bilateral agreements has proven inadequate in addressing the escalating challenges of counterfeiting, ethical sourcing demands, and operational inefficiencies. Opti-Flow Manufacturing Solutions, a pioneering leader in precision industrial components, confronted these systemic vulnerabilities head-on, embarking on a transformative journey by strategically adopting blockchain technology.
Opti-Flow’s path, marked by careful evaluation, a focused pilot, and a phased rollout, illustrates how a permissioned blockchain solution, specifically Hyperledger Fabric, can serve as a foundational layer for verifiable trust. By meticulously logging critical data points – from raw material origins and production parameters to quality control results and shipment details – Opti-Flow created an immutable, shared record of every product’s journey. This distributed ledger eliminated data silos, enhanced end-to-end visibility, and provided an unquestionable audit trail. The integration of smart contracts further automated key processes, from quality gate enforcement to expedited payment releases, significantly boosting operational efficiency.
The tangible benefits realized by Opti-Flow were profound and measurable. They achieved a remarkable 92% reduction in counterfeit component incidents for their pilot product line, safeguarding their brand reputation and yielding significant cost savings from reduced warranty claims. Dispute resolution times with suppliers plummeted by 75%, fostering stronger, more transparent partnerships. Furthermore, the blockchain solution dramatically streamlined compliance audits and provided verifiable proof of ethical sourcing, positioning Opti-Flow as a leader in corporate responsibility. While the implementation journey presented its share of hurdles, including technological integration complexities, data privacy concerns, and the critical need for change management, Opti-Flow’s proactive and strategic mitigation efforts ensured successful adoption.
Looking ahead, Opti-Flow envisions the blockchain as the bedrock for an even more intelligent and resilient supply chain. Future integrations with AI, machine learning, and IoT sensors promise predictive analytics, real-time monitoring, and comprehensive digital twins, propelling them towards a new era of optimized demand forecasting and proactive risk management. Opti-Flow’s story is a compelling blueprint for manufacturers seeking to transcend the limitations of traditional supply chain models, demonstrating that by embracing innovative technologies to build verifiable trust, organizations can not only mitigate risks and enhance efficiencies but also unlock new avenues for growth, differentiation, and leadership in an increasingly interconnected global economy.
Frequently Asked Questions About Blockchain Adoption in Supply Chains
Q1: Is blockchain technology only beneficial for large multinational manufacturers, or can smaller businesses also leverage it?
While large multinationals like Opti-Flow have the resources for extensive implementations, blockchain benefits are increasingly accessible to businesses of all sizes. Smaller and medium-sized enterprises (SMEs) can participate in consortium blockchains initiated by larger anchor companies (like Opti-Flow inviting its smaller suppliers) or leverage ready-to-use “Blockchain-as-a-Service” (BaaS) platforms offered by cloud providers. These BaaS solutions significantly lower the barrier to entry by abstracting away much of the technical complexity and upfront infrastructure costs, allowing SMEs to gain benefits such as enhanced traceability, verified authenticity, and improved access to finance through transparent record-keeping.
Q2: How long does it typically take to implement a comprehensive blockchain solution for supply chain management?
The implementation timeline can vary significantly based on the complexity of the supply chain, the number of participating entities, and the scope of integration with existing systems. A focused pilot project, like Opti-Flow’s, can take anywhere from 6 to 12 months to design, develop, and deploy. Scaling a comprehensive solution across an entire global supply chain, involving numerous suppliers and product lines, is a multi-year endeavor, often spanning 2 to 5 years, as it requires continuous integration, onboarding, and optimization. It’s a journey of digital transformation rather than a one-off project.
Q3: What are the primary data privacy concerns when sharing supply chain information on a blockchain, and how are they addressed?
Data privacy is a paramount concern for businesses sharing potentially sensitive information on a blockchain. While blockchains are often perceived as fully transparent, enterprise-grade solutions typically use “permissioned” networks, where participants are known and authorized. Privacy is maintained through several mechanisms: 1) Access Control: Strict permissions ensure participants only see data relevant to their specific role or interactions. 2) Channels: In platforms like Hyperledger Fabric, private channels allow subsets of participants to transact confidentially. 3) Off-Chain Storage: Large or highly sensitive data (e.g., proprietary formulas) are stored in private, encrypted databases off the chain, with only a cryptographic hash or pointer recorded on the ledger for verification. 4) Zero-Knowledge Proofs (ZKPs): Emerging cryptographic techniques like ZKPs allow one party to prove they possess certain information without revealing the information itself, offering a robust solution for verifiable compliance without exposing sensitive details.
Q4: How does blockchain contribute to making supply chains more sustainable and ethical?
Blockchain significantly enhances sustainability and ethical practices by providing immutable and verifiable proof of origin and compliance throughout the supply chain. Manufacturers can track raw materials back to their source, ensuring they are ethically mined (e.g., conflict-free minerals) or sustainably harvested. Smart contracts can automate the verification of environmental certifications, labor practice attestations, and carbon footprint data, making it easier to identify and address non-compliance. This transparency builds trust with consumers and regulators, enables more accurate reporting on Environmental, Social, and Governance (ESG) metrics, and empowers businesses to actively manage and improve their ethical footprint across their entire network.
Q5: What is the biggest challenge manufacturers face when trying to adopt blockchain for their supply chains?
While technological integration and cost are significant, the biggest challenge often lies in change management and fostering ecosystem adoption. A blockchain solution requires multiple independent organizations (suppliers, logistics providers, distributors) to collaborate, share data, and adapt their processes. Overcoming resistance to change, gaining buy-in from all stakeholders, ensuring data input discipline, and establishing a robust governance model for the consortium are often more complex than the technical implementation itself. Successful adoption hinges on clear communication, demonstrating tangible benefits to all participants, and providing comprehensive training and support to drive collective commitment.
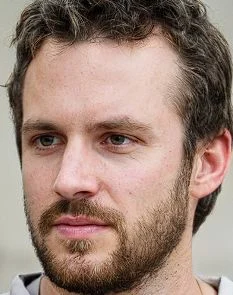
Tyler Matthews, known as “Crypto Cowboy,” is the newest voice at cryptovista360.com. With a solid finance background and a passion for technology, he has navigated the crypto world for over a decade. His writing simplifies complex blockchain trends with dry American humor. When not analyzing markets, he rides motorcycles, seeks great coffee, and crafts clever puns. Join Crypto Cowboy for sharp, down-to-earth crypto insights.